Con questo articolo analizzeremo la fase produttiva principale per un’azienda cosmetica ovvero l’attività di produzione bulk. Come visto nei precedenti articoli, che analizzano le fasi precedenti, arriverà alla nostra postazione (per esempio al turboemulsore) uno o più contenitori contenenti tutti i sacchetti di materie prime pesati dal reparto pesatura e dedicati alla carica da produrre. L’operatore dovrà riempire, seguendo la scheda produttiva e le indicazioni del laboratorio/industrializzazione (seguendo pedissequamente la ricetta), la macchina con le quantità di materie pesate, utilizzandole nel modo opportuno e con i tempi decisi.
Come assicurare l’operazione garantendo il minimo errore?
Avere un dispositivo che guida l’operatore in questa delicata fase è fondamentale e deve garantire due aspetti fondamentali:
- L’operatore deve utilizzare (consumare) i componenti corretti
- L’operatore deve eseguire i passaggi nell’ordine corretto
Tutto questo potrà sembrare una banalità ma, in un ambiente produttivo, con tanti componenti e materie prime presenti, la perfetta esecuzione di queste due attività non è una cosa così semplice. Gli operatori inoltre devono rispettare sia un grado di produzione adeguato sia il rispetto delle GMP, che consistono in una serie di principi per garantire la qualità produttiva. A questo punto possiamo domandarci: come lo si può fare tutto questo nel modo più preciso possibile?
Caratteristiche del dispositivo
Per prima cosa dovremo fornire all’operatore un dispositivo leggero e flessibile, che visualizzi nel momento giusto le poche informazioni essenziali per la buona riuscita dell’attività e che, oltre a visualizzare, possa permettere di fornire input rapidi come potrebbero essere le letture dei barcode stampati in pesatura. Inoltre il display (sicuramente di tipologia touch) dovrà poter ricevere azioni anche indossando guanti di lattice.
Il dispositivo ideale potrebbe essere un wearable di questo tipo oppure un lettore barcode leggero e semplice da usare come lo Zebra TC21/TC26.
Che sia uno o l’altro la schermata principale del flusso potrebbe quello riportato più sotto.
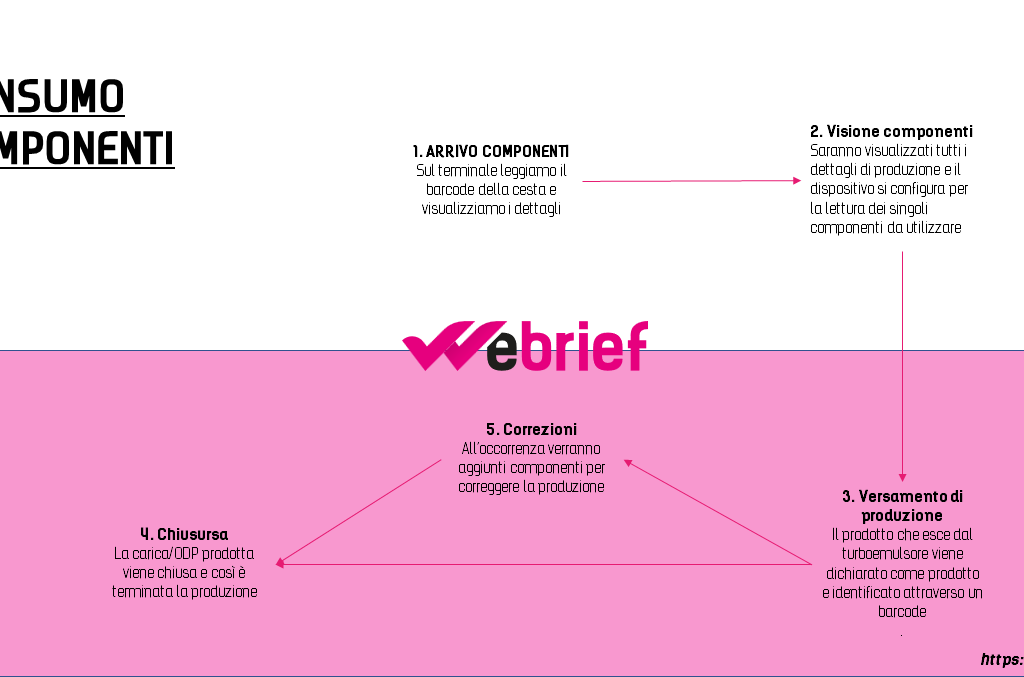
Garanzia dei componenti corretti
Ogni componente prelevato dalla cesta e caricato nel turboemulsore dovrà passare dalla lettura del proprio barcode (stampato e abbinato in pesatura); questo passaggio riesce a garantire, in tempo reale, il corretto prelievo del materiale da utilizzare. Il software dovrà eseguire uno scarico della quantità del componente dal magazzino “PESATO” togliendo in tempo reale il componente dalla giacenza ed eventualmente caricare il materiale nel magazzino WIP della macchina identificata per la produzione. In questo modo, a livello informatico, avremo le giacenze delle materie prime o semilavorati aggiornate tempestivamente; il flusso è quello che potete vedere in immagine di copertina dell’articolo.
Se il barcode letto non dovesse far parte della lavorazione in essere o, per un caso estremo, dovesse essere prelevato in un momento non idoneo il dispositivo dovrà segnalare all’operatore l’avvenuta anomalia e bloccare qualsiasi altra operazione con un avviso adeguato.
Analizzeremo il flusso operativo da seguire e che il software utilizzato dovrà gestire adeguatamente per garantire il pieno successo delle operazioni di produzione.
Flusso principale
Fase 1: Arrivo cesta con componenti
La prima operazione da eseguire è la lettura del barcode relativo all’ODP (ordine di produzione) e alla carica abbinata alla cesta portata in postazione. Se questo non dovesse essere il primo ODP da produrre dovremo avvisare sia l’operatore che il magazzino dell’anomalia in modo da garantire un tempestivo intervento di correzione. La lettura dell’ODP avvierà il segnale di apertura produzione al sistema gestionale. In questo modo potremmo stabilire l’inizio delle operazioni e visualizzare tutte le fasi produttive memorizzate a partire dall’ordine di produzione.
Fase 2: Visione dei componenti divisi in fasi di utilizzo
Il dispositivo in postazione dovrà, una volta letto l’ODP, visualizzare il primo componente da prelevare e utilizzare nel turboemulsore. Oltre alla prelevazione del componente potranno essere visualizzati i vari passaggi da eseguire così da seguire perfettamente i metodi di sviluppo creati dai reparti ricerca e industrializzazione. Tutto questo permetterà anche di sapere a che punto della formula si è giunto ed i tempi di lavorazione corretti.
Fase 3: Versamento di produzione
Con la macchina avviata si provvederà a “scaricare” il prodotto semilavorato (il bulk) in appositi contenitori. Questa operazione potrà essere tracciata attraverso un’apposita procedura del terminale che permetterà di eseguire le seguenti operazioni:
- Scarico del magazzino WIP dei componenti utilizzati (operazione facoltativa)
- Carico del magazzino di output della macchina con il prodotto (bulk) per i chilogrammi indicati dall’operatore
- Stampa dell’etichetta del bulk con i dati identificativi del prodotto (e relativi barcode pronti per la lettura nella fase di riempimento)
Fase 4: Chiusura ODP e carica
La chiusura o sospensione dell’ODP permetterà all’operatore della macchina di rilevare i dati di chiusura e tracciare così l’effettivo tempo di produzione. Questa operazione, se non fatta precedentemente durante il versamento di produzione, andrà a scaricare i componenti dal magazzino WIP della macchina e a caricare l’eventuale prodotto bulk. Queste operazioni di carico/scarico saranno parametrizzate lato gestionale attraverso l’opportuna configurazione del reparto/macchina. Più si riuscirà a mantenere il tempo reale e più i controlli potranno essere effettuati mantenendo una visione globale e tempestiva.
Fase 5: Correzioni
Potranno essere eseguite anche delle correzioni sul bulk aggiungendo/togliendo vari componenti. Tali operazioni dovranno essere tracciate per capire quanto queste influenzano la produzione e quanto frequentemente avvengano.
Controlli Qualità
Durante la produzione il sistema avviserà l’operatore di ogni controllo da eseguire seguendo la scheda produttiva e le procedure di produzione. Anche questi saranno imputati direttamente all’ODP così da poter risalire, come per le correzioni, a tutte le attività di controllo eseguite.
Statistiche e dati produttivi
Infine, avendo rilevato i dati di produzione potremmo sbizzarrire la nostra fantasia e creare le statistiche che più interessano l’azienda. Tra quelle classiche potremo avere:
- Tempi medi di lavorazione divisi per texture
- Tempi medi di produzione per cliente/reparto/macchina
- Costo del personale attribuibile ad ogni ODP
- Componenti maneggiati durante la produzione
- Componenti aggiunti e modificati durante la produzione di un ODP
- Numero di correzioni e di controlli qualità per ogni ODP/reparto/macchina
Ci sarebbero anche altre informazioni relative al personale, alle macchine, alle manutenzioni, ai tempi produttivi ed altro. Per il momento ci fermiamo qui e vi rimandiamo al nostro sito per eventuali informazioni aggiuntive.